Sometimes, a standard crawler excavator just isn’t enough. Some construction projects require a few years to reach completion. Mining, however, requires decades and so they need huge pieces of equipment that remain on-site.
Mining projects make use of some of the largest machines ever built like the dragline excavator for instance.
Introduction and Brief History of Dragline Excavator
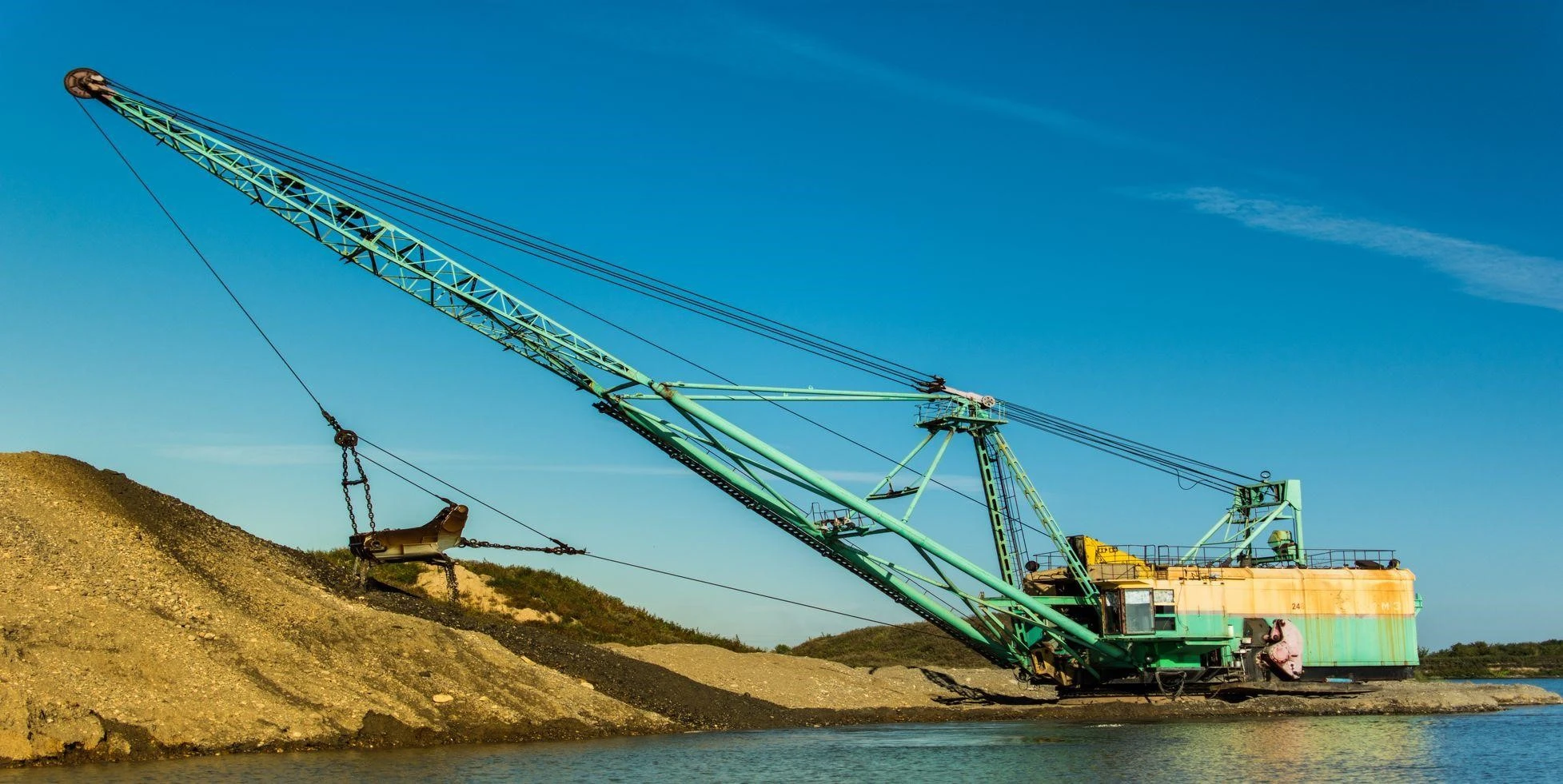
A dragline excavator is a type of excavator that uses a bucket attached to a truss-like structure and a hoist system to excavate material and dump it at a short distance away.
It does this more rapidly than standard excavators. The material can then be taken off-site or to a different location. Draglines are very productive and some draglines can complete a dig-dump cycle in one minute or less.
A dragline excavator is one of the largest machines ever built. This monster digger uses a hoist rope system to raise and lower the bucket while the dragline which is attached to the other side of the bucket pulls the bucket towards the driver hence the name “Dragline excavator”.
As I said, this class of machines is among the largest machines and because of their weight, only the smallest of dragline excavators use crawler tracks.
Instead, the larger dragline excavators, most of which weigh up to 8000 tonnes, use a system where they sit on two large shoes that distribute the weight.
These shoes, can in turn, be attached to electric cams which allow the dragline to “walk” although very slowly. Draglines are mostly used in opening pit mining where they can be operational for decades remain highly productive and relatively low-cost over the time of its operational life span.
The very first dragline was invented by contractor John. W. Page in the year 1904. It was to be used to dig the Chicago Canal. Mr John. W. Page was a partner of the firm Page and Schnable Contracting.
Page soon created the Page Engineering Company to build draglines and by 1923, Page had built its first walking dragline. In 1924, Page produced the first diesel engines that were used solely for draglines.
Mr Page had competitors in the dragline market. One of such competitors was Mohnigan’s Machine Works of Chicago. In 1908, Mohnigan was renamed Mohnigan Machine Company and in 1914, one of Mohnigan’s engineers developed the Martinson Tractor; the first walking mechanism for draglines.
The mechanism was installed on a Mohnigan dragline and by 1925, the mechanism was updated by removing the drag chains for shoes and changing to a cam wheel running in an oval track, giving the shoe an appropriate elliptical motion.
Mohnigan debuted the first dragline using the new mechanism in 1926 and Mohnigan had become so popular for draglines that Mohnigan became a nickname for draglines.
In the 1930s, Mohnigan approved the sale of shares to a company called Bucyrus-Erie and Bucyrus-Erie soon bought a controlling interest the company soon became known as Bucyrus-Mohnigan, and the companies were formally merged in 1946.
After WW1, demand for excavators increased, and a company called Ransomes and Rapier reached an agreement to build Marion draglines.
What’s a Dragline Excavator used for?
Draglines generally fall into two categories; draglines based on standard lifting cranes and larger draglines that have to be built on-site.
Most crawler cranes can serve as a dragline once you add a winch drum. This type is used to build roads, bridges, and ports. This type is built offsite and is transported to the mine/site.
They can be easily disassembled and reassembled.
The other type of excavator is much bigger and heavier. It’s so heavy that transporting it would cost too much and thus, this type of excavator has to be built on-site.
These bigger draglines are meant to stay in one location and remain operational for decades. These on-site draglines are best suited to open-pit coal mining and oil sands strip mining. They can also be used to dredge canals and ponds.
How does a Dragline Excavator work?
The crane-type dragline works by twisting up to the jib and then releasing a clutch on the drag cable. This causes the bucket to swing. Once the bucket passes the vertical, the bucket is thrown by releasing the clutch.
Some operators can make the bucket land about one-half the length of the jib further away than if it was just “dropped”. This practice, however, is not common with large draglines.
The on-site dragline works in a simple way. The bucket is placed above the material to be excavated using the hoist rope. The bucket is lowered and the dragrope is used to drag the bucket along the surface of the material.
The operator then lifts the bucket using the hoist rope and and moves the bucket to the place where the material will be dumped. The operator then uses the dragrope to tilt and empty the bucket.
The drag bucket is fitted with teeth to boost excavation but still, draglines are best suited to materials that have been blasted or softer materials.
What are the limitations of a Dragline Excavator?
Draglines usually have a very high capital cost but there are still very useful in mine operations because of their speed and reliability over many years and their very low cost of waste removal.
When it comes to draglines, the main limitations are both the height and length of the boom. This directly affects where the dragline can dump its load.
Also, how deep the dragline can dig is directly affected by the length of the rope the dragline can use. Draglines are most efficient when digging and removing material below the level of their base.
Draglines can dig above themselves but do so with a lot of inefficiencies.
How much is a Dragline Excavator
Dragline excavators are among the largest pieces of machinery ever. Their huge size and operational capacity over decades make it obvious why they would cost a fortune to purchase. In fact, some major dragline manufactures and their average dragline prices include :
HEC | Price ($$$) |
Caterpillar | 50 – 100 million |
Bucyrus-Erie | 50 – 100 million |
Liebherr | 50 – 100 million |
Komatsu | 50 – 100 million |
Joy Global | 50 – 100 million |
How big is a Dragline Excavator
Draglines are generally huge machines. The standard crawler crane type of draglines is the smallest of the bunch. They typically weigh;
On-site draglines are huge with the average size of a dragline weighing about 8000 tonnes.
The average bucket size ranges from 40 yards to 80 yards and 148-328 feet. In one cycle, a dragline excavates up to 450 tonnes of material, and some draglines can complete a digging cycle in about a minute.
Dragline Excavator uses and applications
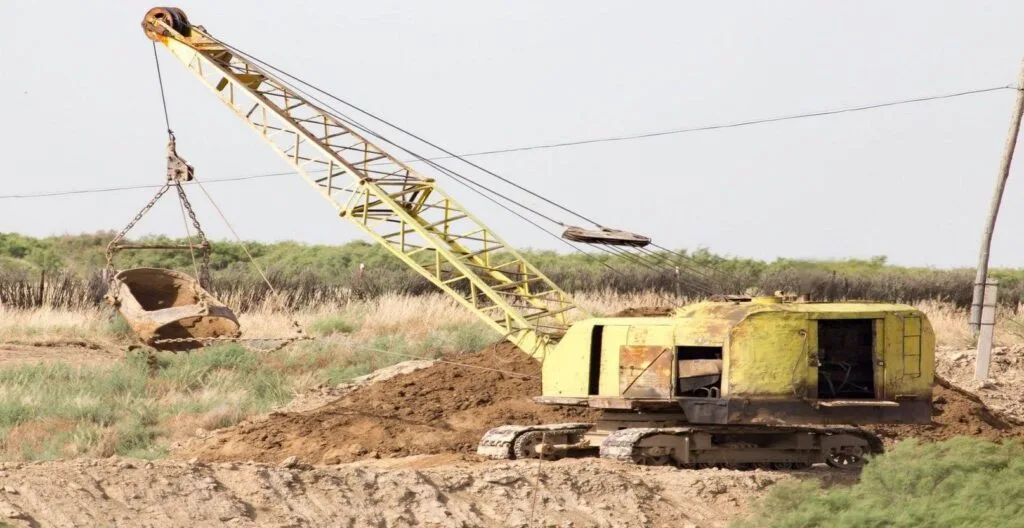
Draglines aren’t as popular as they used to be some decades ago. This is due to the huge capital cost involved in running a dragline plus their energy demands are so great that it usually costs thousands of dollars per hour to run a dragline excavator.
However, smaller draglines are still very popular today as draglines have a wide range of applications in modern civil engineering projects.
Some very common applications of smaller draglines include :
- Building roads
- Building ports
- Building bridges
Larger draglines are even less common today although they remain quite popular in the mining industry as mining projects often remain in service for decades.
Some popular applications of large draglines in mining today are :
- Removing overburden I.e removing anything in the way of the real product e.g coal mining and oil sands strip mining
- Dredging canals and ponds
- Deep pile driving
- Road excavation
Draglines vs Regular excavators (Advantages vs Disadvantages, Differences) :
Although dragline excavators and regular hydraulic excavators are both powerful diggers, they do have some fundamental differences that make them best suited to different types of jobs.
The major differences between a dragline and a regular excavator include :
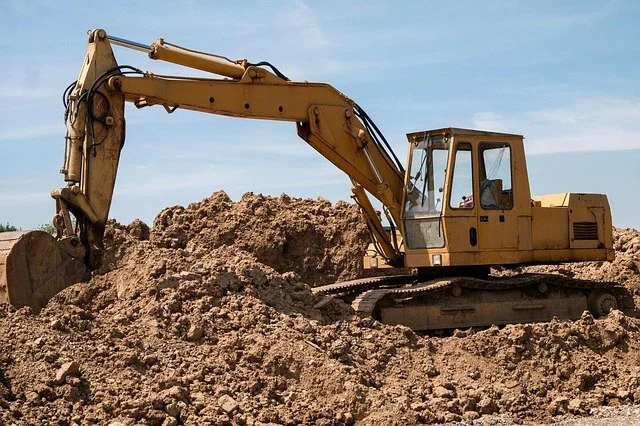
Size: Draglines are generally larger and heavier than other types of excavators. In fact, they are among the largest types of excavation machines. On-site draglines weigh up to 8000 tonnes on average while regular hydraulic excavators only weigh up to 90 tonnes on average.
Their huge size means that only the smallest types of draglines can be transported on roads as most draglines have to be built on-site. Excavators on the other hand can be transported using flatbed trailers.
Power consumption: Most regular excavators use a hydraulics system that is powered by a diesel engine while dragline excavators require so much energy to run that they have to be connected directly to the local power supply. This adds significantly to the power costs of the operation.
Speed: Walking draglines, due to their immense weight, can only move very slowly and are able to move only a few meters per minute while regular excavators on the other hand are much faster.
This is important because, if your project is large or/and it requires that the excavator moves over a considerable distance, then an excavator would be faster and more suitable to such distances.
However, onsite draglines have a long reach and can work a large area from the same position so, they don’t need to move along the site as much as smaller machines.
How Much Does a Dragline Bucket Hold?
There are different sizes of dragline buckets. The most common size range for dragline excavator buckets is; 40 to 80 cubic yards (30 to 60 cubic meters), however they have been extremely big buckets that have reached up to 168 cubic meters.
Important Manufacturers Draglines
Although the demand for draglines has dropped due to the drop in the demand for coal, draglines still remain popular with open pit mining operations. The major manufacturers of mining draglines have reduced considerably since the 1960s but a few major players remain.
- Joy Global
- Komatsu
- Caterpillar
- Liebherr
What is a walking dragline excavator?
A walking dragline excavator is a dragline excavator that uses a set of pontoons and an in-built walking mechanism to “walk” at a very slow pace, usually a few meters per minute as the feet have to be repositioned for each step.
Apart from the smallest draglines, all other draglines use this “walking system” as they’re so immensely heavy that caterpillar tracks would put too much pressure on the ground and wouldn’t be able to handle the weight of the dragline.
Fortunately, these draglines have a long reach and can work on a large area from a single position at a time so they don’t require as much movement as regular excavators.
Biggest Dragline Excavator in operation
The biggest dragline excavator ever built was named “Big Muskie”. It was manufactured by “Bucyrus-Erie” in the year 1969 and it was in operation from 1969 until 1991. It featured a bucket of 220 cubic yards and a boom length of 310 feet.
It weighed about 12,000 tonnes and was supplied 13,800 volts of electricity through a trailing cable which had it’s own transporter and coiling units to move it. It moved very slowly at 0.1 mph on its two hydraulic feet.
The entire machine took 2 years to build and cost $25 million in 1969 which is equal to $176 million today after adjusting for inflation. Its operations came to an end in 1991 due to high operating costs, rapid drop in demand for high-sulfur coal, and public opposition to strip mining in Ohio, and as such, it became too expensive to run.
It remained inoperative for another 8 years until the EPA and the state of Ohio moved to enforce the Surface Mining Control and Reclamation Act. The result was that the Big Muskie was dismantled and sold for $700, 000 to the Mayer-Pollock Steel Corporation.
Draglines today don’t weigh as much as the big muskie but there are still some very large draglines on the market today.
The largest dragline excavators on the market today include :
NAME | BUCKET SIZE (YARDS) | BOOM LENGTH (FT) | DUMPING HEIGHT (m) | DIGGING DEPTH (m) | WORKING WEIGHT (t) |
P&H9020XPC | 110-160 | 325-425 | 64.5 | 76.7 | 7,539-8,002 |
CAT 8750 | 110-152 | 435 | 61.5 | 79.8 | 5,800-7,500 |
P&H 9020C | 117 | 405 | 59.5 | 70.5 | 5,647-6,200 |
Costs of owning and running a Dragline Excavator :
Due to their huge size, high performance, and durability over the operating years, it is no wonder that draglines cost a fortune in capital costs. In fact, a large dragline used in open pit mining costs around $50-100 million to own.
Some of this huge cost is due to the fact that the dragline has to be built on-site.
Also, the electricity costs contribute significantly as most mining draglines require so much electricity that they need to be connected directly to a high-voltage grid at voltage However, the annual operating costs of draglines vary according to the dragline and the project management.
The running cost of an HEC dragline with a 24 cubic meter bucket capacity and a production capacity of 3.6 million cubic meters per year is as follows :
DRAGLINE | OPERATING COSTS PER YEAR | AMOUNT ($) PER ANUM |
HEC Abhimanyu 24/96 | Annual Manpower cost (Salaries and wages in India) | 21,892 |
Power and energy costs based on 13.65MKWH | 900,000 | |
Yearly lubrication costs @30% power consumption | 270,270 | |
Yearly maintenance costs @20% depreciation cost | 135,135 | |
Major breakdown cost | 270,270 | |
TOTAL | 1,599,594 |