The need to save time and money as well as increase the output of excavators has led to the development of a special attachment called a bucket crusher.
It so advantageous in fields of construction, mining, and environmental conservation.
It is a tool that helps recycle debris and produce useful output, a spotlight in reclaiming land with piles of dumped construction material. This article looks at important things that are there to know about this attachment.
What is A Bucket Crusher?
These are attached tools similar to the normal excavator bucket but are designed with jaws for crushing materials on site and are able to produce graded aggregate on site to be re-used.
Bucket Crushers are capable of crushing concrete debris, rubble, masonry, asphalt, natural stones and rocks.
Crushers are self-loading and this grants them the ability to charge and discharge the crushed materials exactly where they are needed.
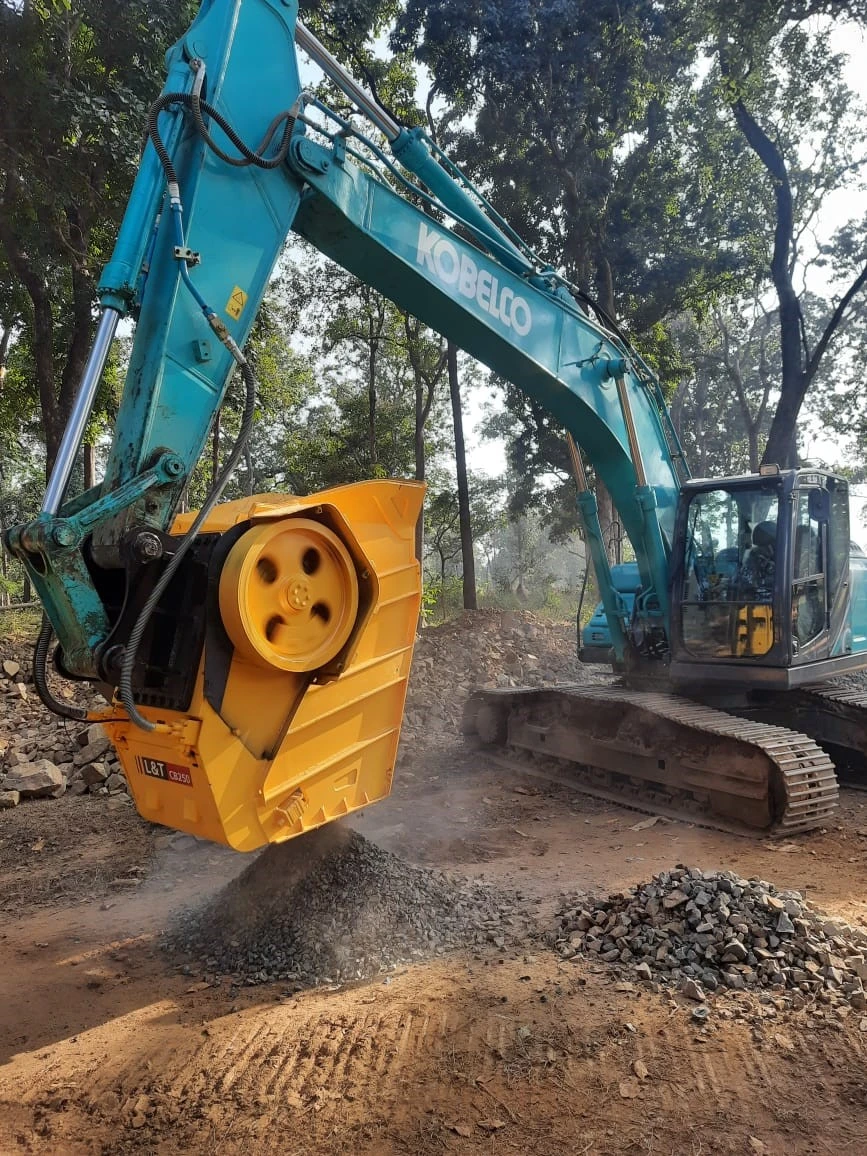
They are also capable of disposing of the rubbles and rubbish created during the process of crushing and also allow the operator to recycle and process all the crushed materials up to 100 tons per hour.
They are designed with an open rare to allow the release of the shredded materials. These attachments vary in size and weight.
It is more efficient when it works together with the breaker. This is because the breaker can tackle large and stubborn materials mostly in quarries and leave the rest to the bucket crusher.
Features Of a Bucket Crusher
- Most take the form of a bucket containing a fixed bottom and a moving jaw with wedges to crush materials against it. But there are several designs of the same.
- Range in size and are therefore suitable for both small and large works. The bucket can hold different capacities depending on brand and size.
- Some contain removable grids that dictate the grade of material output achieved ranging from fine to course grades. this makes it possible to regulate the grain sizes desired.
- They have jaws that are hydraulically powered to give them enough power to crush hard rocks and concrete. A hydraulic motor moves the jaws through an axle.
- Have replaceable wedges that ensure penetration and strength while crushing material.
- Those with reverse functions help eliminate material that would otherwise jam the system. The therefore reduce on stoppage time and risk of damage.
- Bucket Crusher Tools are able to crush various materials including natural stone and rock, masonry, quarry wastes, asphalt debris, as well as concrete debris. They have the ability to do these things at a high speed and reduce them to very small sizes between 3 to 5 inches.
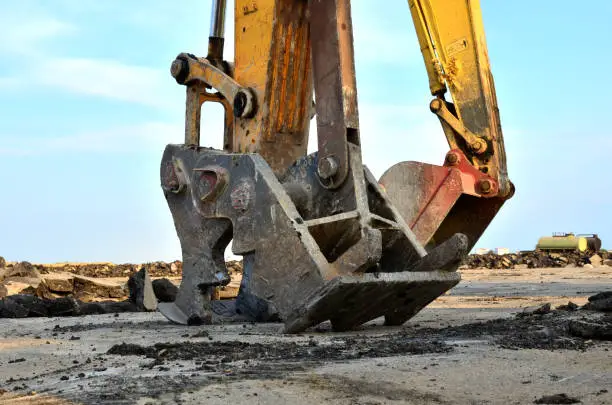
- They are built of hard metal for heavy-duty applications with low maintenance as they deal with bard and abrasive materials.
- There is a magnetic option with electromagnetic iron separator that is easy to attach to the bucket and come with an installation kit.
- They make it possible to reuse debris collected from construction sites on the spot or when latter needed. They therefore reduce on costs of purchasing some construction materials.
How Does A Bucket Crusher Work ?
The jaws of this tools are driven by hydraulic system of the excavator. During the process of crushing this tool is placed vertically to allow the release of the crushed materials at the bottom of the bucket.
The excavator’s hoses for intake and draining are directly connected to this attachment. The correct amount of flow of oil and its pressure is controlled and regulated by a hydraulic valve blockage.
This movement is then transferred and reciprocated to the movable jaw. One of these jaws is fixed while the other one moves.
The one that moves, moves back and forth and crushes the materials against the fixed one and the crushed material enter between the two jaws.
These jaws have a gap between them that range in size of about 970 mm to 1650 mm and it determines the discharged materials size. These jaws are moved by an eccentric element rotated by hydraulic motor and mounted on an axle.
The materials being crushed are fed from the top of the machine.
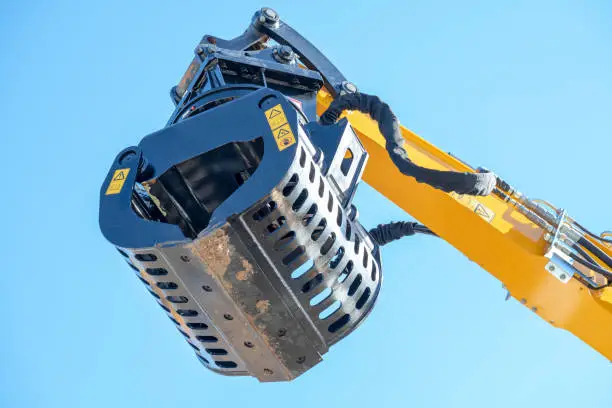
Applications Of A Bucket Crusher
These tools have various areas of application. These are :
- On-site crushing of materials in demolition sites. They reduce the amount of debris obtained from demolition sites by reducing them to reusable sizes and separating different sizes of material.
- Road works and excavation projects.
- Pebble selection in waterways.
- Collecting and crushing rocks at quarries.
- Crushing needs in mines.
- Reducing particle sizes in rocky soils.
- Environmental reclamation by recycling waste material piled up over time or at construction sites.
Advantages Of Bucket Crusher
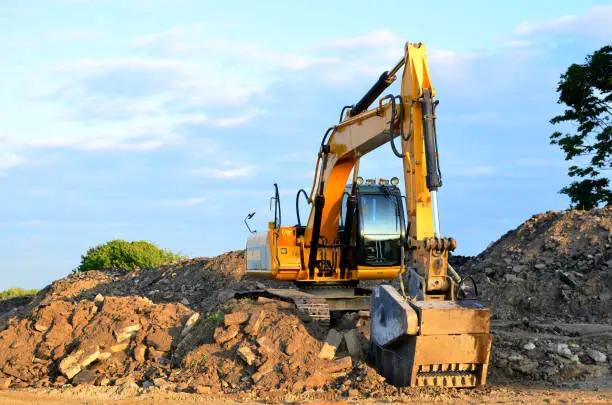
- Easy to use and operate. These are practical powerful attachments with little complications in their use and operation.
- They are convenient in the sense that they are applicable for both small and large jobs in different application areas such as demolition sites, road construction, excavation sites, environmental projects, and utility works.
- Pose a sense of simplicity as they are designed to be easily maintained on the site thus saving on time spent in maintenance issues as well as reduce the space and number of equipment on a site.
- Save on cost as material is immediately recycled on the spot and reused. Transportation and landfill cost is also eliminated therefore generally saves on costs incurred in hauling and purchase of fresh material.
- Bucket Crushers save on time as the operator doesn’t need to wait on other equipment such as skippers or dumper trucks. The attachment is designed to collect the material, process it and move it to require places such as in backfilling.
- Versatile as a single system may be used across different jobs on the site ranging from reducing amount of debris to crushing needs to recycling of natural and waste materials piled up over time on construction sites.
- Profit and sustainability. Material is recycled immediately on site as fast as it is produced giving it new use as fill or base and may be used for future projects. Reselling it also creates revenue and profit.
- It is possible in most brands, to adjust the size of grain produced.
Bucket Crusher In Action :
The 6 Factors To Consider When Selecting A Bucket Crusher
It is important to always acquire a tool that meets your needs and that is reliable to provide high performance and output.
It should be easy to use should have less maintenance needs and reduce operation.
For these to happen, there are several considerations to make as outlined below :
Output requirements :
One should select an attachment that will provide the desired output in terms of particle grades and shapes as well as capacity. The best choice therefore would be the tool that allows for quick grain size adjustments.
Operational considerations :
The type of attachment to be obtained depends on factors such as power demands, maintenance requirements as well as safety.
A good attachment should be favorable in the above-mentioned aspects. Replacements should be easy to do on the site.
Material characteristics :
This refers to the size of the material to be crushed, its material, and its hardness. A good crusher should be able to handle the material you need to work on.
Hard and abrasive materials require a crusher whose teeth are adequately strong and resistant to abrasion.
Size of carrier excavator :
One should select an attachment that does not exceed the carrier’s capacity. It should also pride compatibility to avoid damage.
Information on such may be obtained from websites and manufacturer’s specs on the product.
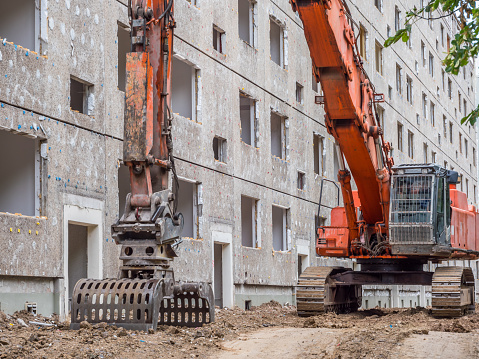
Availability :
One should go for the attachment that is available in the market and whose spare parts and replaceable tools can easily be purchased in nearby outlets.
The manufacturer should also have support staff who can reach the users when need arises.
Design of the machine :
A contractor should look for a machine that contains the most favorable features. They should go for the attachment with reverse function to eliminate debris that would jam the tool.
Those with sliding plates to direct material to the crushing jaws are also an excellent choice.
The 7 Things You Must Do To Maintain A Bucket Crusher :
It is important to ensure that your attachment is in good condition by following the manufacturer’s guidelines and required maintenance intervals.
This will greatly improve the attachment’s uptime and lifespan. Some activities have to be done prior to, during, and after use of the machine.
Most of these are outlined in the attachment’s user manual stating the intervals when each activity should be carried out.
Here are some actions :
- Before running the machine, the operator needs to check the crusher, components and adapter plate for any cracks, deformations, abrasions or damages.
- The operator must inspect the hydraulic lines and transmission housing for any damages or leakages. The hydraulic motor should also be inspected for bubbles and leaks. The connections need to be tightened to avoid the leakages and damage. This should be done regularly
- The jaw bolts and fixing screws of the wedges and tensioner system should checked and tightened if any of the is loose. This is mainly done for the first 50 working hours and repeated on every similar interval.
- Wearing parts should be replaced. The wedge and the jaws should be changed both if the wearing causes effects to the screw head. The belt should also be checked for tension in intervals of 80 hours or less.
- The central greasing points should be lubricated using a grease gun. The operator should check the manufacturers guide to establish the amount and type of lubrication to use.
- Following the operation guidelines is important to increase the lifespan of the tool.
- The attachment should not be used for purposes it was not made for such as excavations. The operator should also avoid crushing oversize materials or non-crushable materials.
- The attachment should be cleaned off any grease and oil buildups as well as debris to ensure smooth performance. This should be done by use of tools and not hand as it would lead to serious damages.
Manufacturers Of Bucket Crushers :
The market today contains quit a number of these attachments from different manufacturers from various parts of the world.
There are so many companies dealing with these tools and we will highlight a number of them.
HYDRARAM :
They produce attachments for demolition, recycling, and green industry. They developed the HCB-Series.
BONOVO :
Based in China. It is a construction machinery industry manufacturing attachments, undercarriage parts, and earthmoving equipment.
SIMEX
The headquarters are in Italy. They are dealers in earthmoving attachments. They are the manufacturers of the CBE series.
MULTITONE
The manufacturer’s headquarters are in Italy.
AJUTECH-OY
They are the manufacturers of Vipermetal crushers.
EPIROC
It is a Swedish company that manufactures mining and infrastructure equipment.
MB (Meccanica Breganzese)
They manufacture jaw-action bucket crushers and screening buckets.
JCB
A British company that manufactures construction and agricultural equipment as well as demolition and waste handling equipment.
GENESIS
Are the manufacturers of the GBC series?
L&T (Larsen Toubro)
It is an Indian company and is the manufacturer of the L&T CB250.
Conclusion
Fitting this tool to a compatible machine will produce results that will exhibit great benefits in the collection, crushing, and movement of all the discussed materials.
It is therefore a very important attachment that is important to acquire and put to good use. It is important for contractors to do their research on the attachment of the best fit and speak with the manufacturers on how to get the best out of the attachment.
Testing out the machine first will help users take the right steps towards maximizing benefits and reducing costs.
Proper maintenance of the attachment will improve results and give it a long lifespan. You may also read Rock Breaker