There are different ranges of sizes of rock breakers, from mini, through medium to large hydraulic breakers. There are also various shapes of Rock Breaker chisels or tips that are applied in different ways during operations.
Tapered flat or wedge-shaped, moil pointed and flat or blunt-ended chisels are common in use
Tapered flat rock breaker chisels are commonly used for general demolition activities such as cutting and penetration activities including trenching and slope finishing.
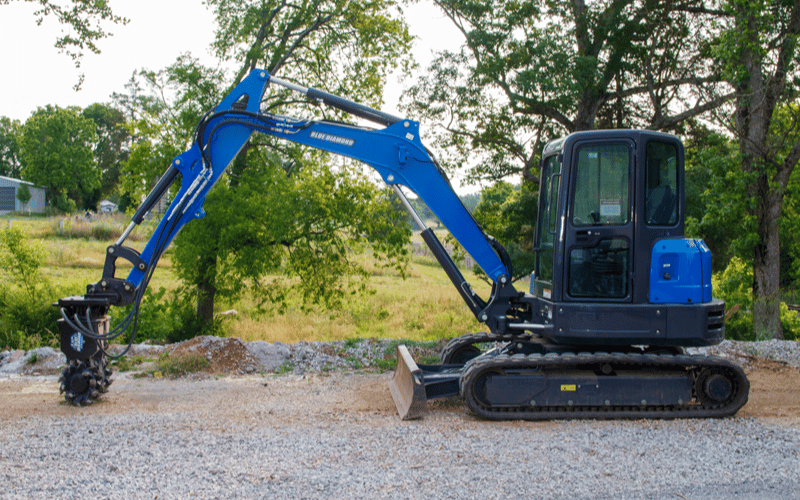
The moil pointed chisels are also used for general demolition but more specifically for breaking concretes or hard rock strata.
Flat ended chisels normally take cylindrical shapes for their torso and a flat circular surface at the end. They are mainly used to impact breaking activities such as scaling in mining or secondary rock breaking.
How Does A Rock Breaker Work?
A hydraulic breaker has different parts that that are mechanized together to produce successful work
The tie rods, the nitrogen chamber, the main valve, piston, the front cap and the working tool or chisel.
Its operation is achieved by an incompressible hydraulic oil that is stored within it, which efficiently transfers energy with no accountable lose .
The hammer starts working when the main valve in the cylinder allows the hydraulic oil to pass through it during the upward stroke.
The upward stroke releases pressure in the upper chamber so that the piston is pushed upwards by the pressure in the lower chamber due to pressure difference.
When the piston opens the main vale as it reaches maximum height due to the upward stroke.
The main valve allows flow of the hydraulic oil into the upper chamber to make it a high pressure zone.
This forces piston downwards again due to energy built up in the nitrogen gas chamber.
The downward movement is the stoke cycle that causes impact. The energy is transferred by the hydraulic fluid to the working tool or chisel that is used for various activities.
If I have to take you to engineering principles, the hydraulic hammer simply applies the Pascal’s Law of hydraulics
Pascals Law : ” The pressure applied at one end of an enclosed incompressible fluid is transferred equally to all other parts of the fluid. ”
How Much Does A Rock Breaker Cost?
Hydraulic breakers come in ranges of sizes and their cost is proportional to their sizes and features.
The price also differ regionally globally.
In India for example, a rock breaker can cost from as low as around Rs 530 000 to as high as beyond Rs 20,00,000.
What Are The Rock Breaking Techniques?
Major techniques are penetrative breaking and impact breaking.
Penetrative breaking usually require moil pointed or wedge shaped tool with lesser energy compared to impact breaking that require a tool with a blunt end.
Rocks are usually broken in two phases :
- Primary Breaking
- Secondary breaking
Primary breaking is the initial stage of rock breaking from the parent rock material that has established well in the underground.
This operation require high impact. A breaker with high impact power is highly recommended .
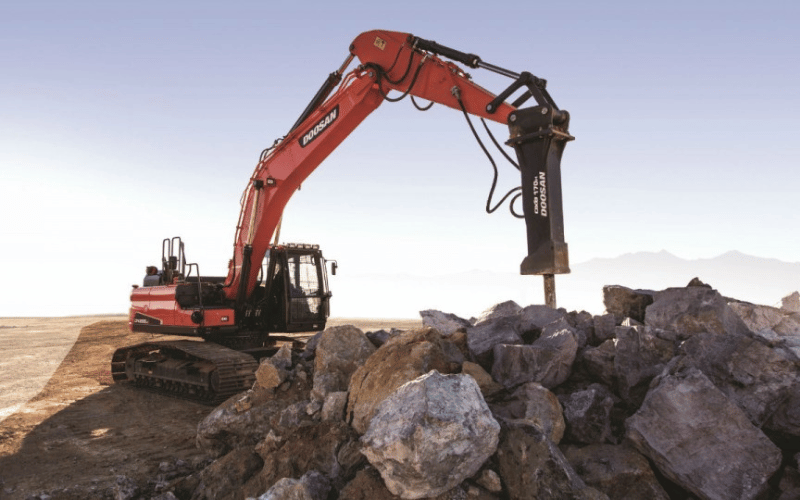
Such breakers characteristically have pistons with large diameters and long stroke designs.
In secondary breaking phase, the large rock materials that are broken from the parent rock are further broken into smaller pieces.
This phase require less impact as compared to the former and wedge shaped working tool is recommended .
Before starting any work that require the hydraulic hammer, the first principle step is to load the hammer.
The hammer of the excavator is attached to the far end of the boom arrangements using the tie or side rods .
After loading the hammer, the operator applies a downward force to slightly raise the front of the excavator machine. Finally, the operator presses the control lever or the foot pedal to start the hydraulic breaker.
Working Of A Rock Breaker :
Types Of Rock Breakers
Rock breakers are categorized into two major types :
- Mobile Hammers
- Stationary Hammers
Mobile rock breakers are normally located on the slew frame.
They are mainly use during underground mining to reach the deposits of hard rock and crush the coarse ore into smaller sizes for transportation. This is also done while trenching.
Stationary hammers are attached at the pedestal and they are preferably used breaking bigger harder rock materials.
It is majorly applicable in mining sites, cement industries, industries that deal with coal and thermal power plants.
How To Select A Rock Breaker
Proper selection of the hydraulic hammers for the most relevant job helps to optimize the efficiency and performance of the equipment.
Whether you are going to blast rocks or break a concrete, there are key features and considerations to take note on during selection and purchase of a rock breaker.
Number of Components
A rock breaker with fewer number of components and moving parts makes it is easier to carry out maintenance practices. It is less bulky and reduces the cost of operation to enhance reliability of the hammer.
How the Hammer is Powered
When the hydraulic breaker has a dual power source, the hydraulic and gas energy are combined while the recoil energy is absorbed and saved for the next blow, this increases the intensity of the impact.
Noise Reduction Mechanisms
Breaking rocks or carrying out any demolition activity can cause a lot of noise.
Always consider a hammer with noise reducing brackets.
Typically, a hammer with short side bolt and vulcanized rubber sleeves or protected thread will lead to reduced vibration and less noise that is environment friendly.
Versatility and Sensitivity to Back Pressures
When the hammer accommodates different kinds of chisels, it is applicable in many tasks without much strains.
Low sensitivity to back pressures makes the hammer fit for many excavators without any requirement for accumulation of high pressure line.
Hammers that operate at lower pressure have longer lifespan and operate at lower costs.
Main material of the Body
The strength of material used to make the rock breaker determines its survival in various environment and weather conditions.
Steel that has undergone proper heat treatment makes a better material for hammers as it does not easily depreciate in quality and strength under adverse environmental conditions.
Manufacturing Company
Buying hydraulic hammers from a reputable company like Komatsu will save you a great deal.
Komatsu has grown so stable and reliable, and they offer repair services globally in the world network.
Okada and Kobelco also have outstanding brans of hydraulic breakers.
Okada specifically produce the breaker whose piston have large diameter which are significantly applicable for primary phase of breaking.
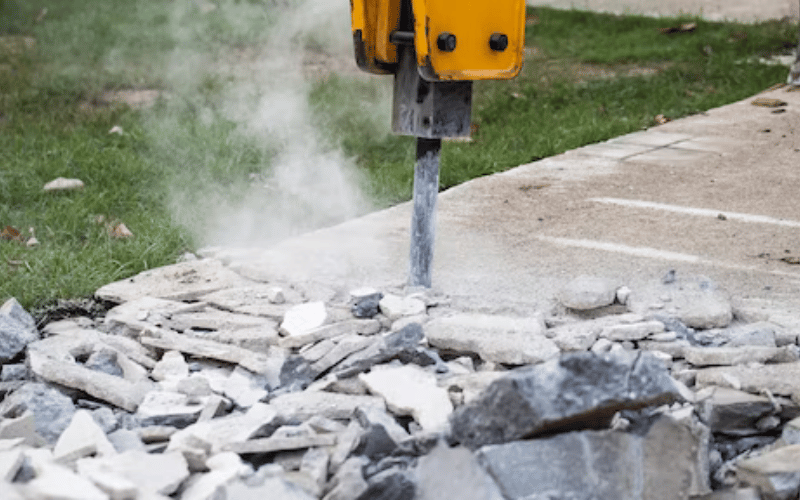
How To Mount A Rock Breaker
Mounting the hammer to the boom is an important aspect of safety awareness measures during operation that must be appreciated at all costs.
The principle thing is compatibility of the rock breaker and the carrier.
Compatibility is subject to the weight of the hydraulic hammer and that of the carrier.
Before mounting the hammer, take note of the weight to ensure that the excavator will remain stable during the whole period of the operation.
Only mount the weight that the excavator can carry to ensure safety at the working site.
The kits for mounting typically include the rock breaker mounting bracket, the hoses that connect to the hydraulic system of the carrier, and you may also need the flow control valve.
The top bracket and the bolt package are also necessary materials of the kit.
Other accessories that are essential during mounting include :
- The Male Adapter
- The Male disconnect
- The Female disconnect
- Hex Head Cap screw
- Hex nut
- Pressure hose
- Return hose
- Link pin
- Klik pin.
Rock Breakers In Action
When mounting the hydraulic breaker, place it horizontally on a raised platform structure, preferably wooden blocks.
The boom pin holes are then aligned and the stick pin is installed first, followed by the cylinder link pin.
Next, connect the hydraulic pressure hose on the left followed by the return hose on the right and lastly, let the shut-off valves open.
When demounting the rock breaker from the carrier, first release the pressure, closing it completely as well as the return line shut-off valves.
Before you lay the hydraulic breaker down, disconnect the hydraulic hoses first.
Next, the pressure and return lines on the excavator are sealed and the whip pressure hose and the whip return hose are connected respectively.
Finally, put the hammer in a horizontal position on wooden blocks to remove the boom pins.
How To Improve The Performance Of A Rock Breaker :
The performance of the hammer can be optimized by using it in the most correct way, while following the routine maintenance practices as the manufacture’s manual require and indicate.
The major operations of the hydraulic breaker require thrusting force, therefore, it is important to know how to give effective thrust and master how to direction the thrust.
When the thrust is very low, the impact energy will not be sufficient enough to break the rock.
Conversely, when too much thrust is applied, more vibrations are caused, the broken rock may fly away and cause injuries to other people on the site and to the operator himself or even damage part of the excavator.
Direction of the thrust should be perpendicular to the chisel to protect the piston from breaking and prevent any slipping of the tool.
When the operator continues to hit the rock when the tool or chisel is absent, all the pressure and shock is directly transmitted to the parts of the breaker.
This is the aspect of blank firing and it can cause great damages to hydraulic hammer by breaking the bolts, even instantly.
What Are Key Safety Measures When Using A Rock Breaker ?
Safety when using the hydraulic hammer can be achieved by ensuring self-safety and making proper observations on the working site and the entire environment for any health hazards .
Make sure that the bed rock is strong enough to carry the excavator in a stable state throughout the working session.
The operator must ensure that the weight of the hammer is compatible with the carrier to make sure that it is stable during the work.
Do not hold or touch the breaker or the tool when the boom is in motion.
The operations, mounting and demounting of the hammer normally require an assistant who must coordinate with the driver or main operator to agree on all directions of motion of the boom prior to any striking.
Do not touch any parts of the hydraulic breaker during operation to avoid burns because the oil gets hot with time. Put the hammer in the correct position while travelling.
Wear protective gear, especially a face shield to keep away flying rocks from reaching your face.
When replacing any worn out parts, use the brand’s spare parts compatibility and efficient fitness of the parts.
When checking for oil leaks, do not trace using your hand, the oil is always under high pressure and can easily make a hole through your finger.
Top 7 Rock Beaker Brands
There are various brands of hydraulic hammers produced by companies across the world .
Some of the renowned companies and models they produce are :
1) Body Plant Services Limited
This company is established in the UK . It is a major dealer in construction equipment and also produces the arrowhead model of rock breakers.
A typical brand from BPS is the “Arrowhead – Model S30 –Hydraulic Rock breaker”.
The S40 brand is made of very high-quality materials and comes with a very viable noise and vibration reduction mechanism.
It has a simple design that makes it easier to do maintenance practices, and it also works at low pressure.
2) Furukawa Rock Drill, USA
This company manufactures blast-hole drills. A typical model is the “Model Fx15/25/35-Hydraulic Rock Breakers”.
3) Changzhou Raymond Precision Machinery Company Limited
It has the established is China and typically produces the model “MODEL RHB140”.